Suppliers Quality Management
The Supplier Quality Management Suite makes it possible to exchange information with the Supplier Chain via the Web in an agile, simple, clear and effective way to provide continuous improvement, elimination of waste and standardization of processes, naturally providing mutual growth. The use of the System Portal brings transparency, agility and perfect control to the Suppliers, transferring to them the responsibility for preventive and corrective actions.
SIQ Suppliers Quality Management Suite is composed of the following modules:
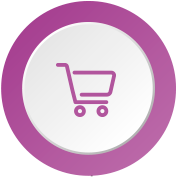
Suppliers Quality Management
-
Compliance (Legal documents, contracts and certifications management)
Control and maintain documents of suppliers of products and services such as Certifications, Licenses, Contracts and other documents according to the quality policy of the Company. Most common examples: ISO 9000, TS 9000, VDA, ISO14000, ROHS, Environmental Licenses, Operating License, Production License, Supply Contracts, Licenses of public agencies such as Federal Police, Military Police, IBAMA.
-
Assessment / Audits
It allows you to implement and manage internal audits in DC and store processes.
It controls results and next audits.
Action follow-up.
Example of audits: Productive Process / Quality System / Sanity. -
Initial Samples Approval Process – own and specific brands)
Management Approval of INITIAL or MODIFIED samples, along the chain of Suppliers, from the issuance of the Request (integrated with the Engineering Document) to the receipt of PPAP. Control of schedule, responsible, deadlines, actions, agreements, results and Status of each project.
-
Packaging Conformity
Control of Packaging starting in the development of the product and following throughout its useful life. Definition of packaging, quantities, standardization, and flow with suppliers. Management of shortages, conditions and excesses.
-
Platform Inspection
It allows you to control the products while they are in the DC and when they leave the DC through sampling tables (parameterizable), skip lot and technical files, automatically generating performance indicators and nonconformity notifications internally.
-
Inspection at Origin
Control the products of the suppliers at the origin, before leaving the place they were manufactured, and often with control during the production process. Management of controlled shipments. All goods shipping will be controlled incorporating aspects of Quality in the Notice of Boarding and Invoice.
-
Non Conformities
The main objective of the Nonconformities module is to identify and completely eliminate all existing Non-Conformities, minimizing undesirable situations with the application of Corrective Actions and Preventive Actions, always focusing on the Continuous Improvement of activities. The module directs users to a methodology for solving nonconformities, according to the method applied by the company, as: 8D, 5PB’s, Ishikawa Fish Diagram, among others, these methods being established according to the client’s preferences.
-
Skip Lot
Inspection of fractional lots of Suppliers products that present an exemplary and stable history of quality, according to criteria of importance defined by the user, such as: characteristics, levels of reliability, etc.
-
Refund
Explain the internal costs generated by problems of poor supplier quality, thus allowing the submission of the request for compensation to the Suppliers.
-
Indicators
Quality Competitive Intelligence. PPM, Average, Standard Deviation, Dispersion, Failure Trends, IDF, Audit Grades. Pareto Charts, Trends and management reports.